Reduce costs and boost efficiency with coded welding for industrial pipework. Invest in defect-free, strong joints that withstand demanding conditions.
Enhanced Strength and Longevity
Coded pipe welding ensures that industrial pipework is constructed to the highest standards regarding strength and durability. Coded welders follow strict procedures set by ASME and BS EN to create high-quality welds that can withstand temperature fluctuations, extreme pressures and mechanical stresses.
A well-executed weld provides a seamless connection between pipe sections and has no weak points that could lead to leaks or cracks. On the other hand, poor-quality welding has a higher risk of having defects that can compromise the pipe’s ability to handle operational demands. Coded welding ensures that these failures are minimised.
Industrial pipelines are often exposed to harsh environments, chemicals, moisture, and fluctuating temperatures. Coded pipe welding helps prevent corrosion by producing smooth, defect-free joints that resist external and internal degradation. Properly welded joints reduce turbulence inside the pipe and minimise erosion caused by high-velocity fluids.
By following strict welding standards, coded welders can extend the life of pipework and reduce maintenance costs over time. High-quality coded welding provides the durability industrial pipework needs.
Improved Safety and Risk Reduction
Coded pipe welding is crucial for maintaining the safety of industrial pipework, especially in high-stress environments such as oil refineries, chemical plants, and power stations. These pipelines operate under extreme conditions and are exposed to corrosive substances, and poor-quality welds can create weak points and increase the risk of structural failures. Coded pipe welding ensures the pipework is free from structural defects and corrosion.
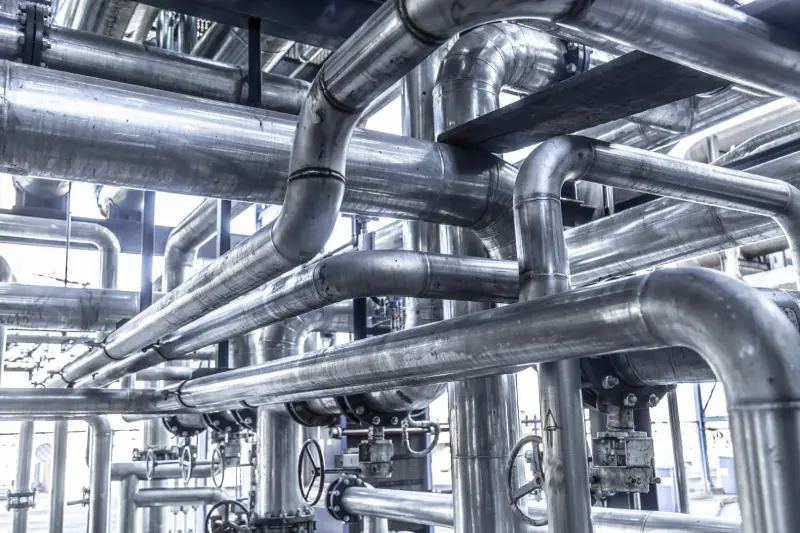
When pipes are welded by coded welders, the joints are formed using industry-approved techniques to minimise issues such as cracks, porosity, and incomplete fusion.
By following strict welding codes such as ASME and BS EN, operators can be confident that their pipework meets the necessary safety standards. This helps prevent unexpected failures and ensures the reliability and stability of industrial systems.
Leaks in industrial pipelines can lead to serious safety risks, including fires, explosions, and exposure to toxic substances. Coded pipe welding helps prevent these hazards by producing high-strength, defect-free welds that can withstand operational pressures without failure.
Coded pipe welding ensures that joints are fully sealed, reducing the risk of leaks developing over time. Certified welders use ultrasonic or radiographic inspections to check the integrity of each weld. This quality control process ensures the pipes are compliant with safety regulations.
Cost Savings and Efficiency
Poorly welded joints are more prone to defects such as cracks, leaks, and corrosion, leading to expensive repairs and disruptions. Coded welding is used to produce stronger and more reliable pipework that can withstand high pressures, corrosive environments and extreme temperatures.
Certified welding techniques help prevent common issues like porosity and incomplete fusion, and reduce the likelihood of failures. This results in lower maintenance costs over time, as well-built pipelines require fewer repairs. Coded pipe welding helps minimise unplanned shutdowns by ensuring that pipelines are built to withstand demanding conditions without failure.
High-quality welds reduce the risk of leaks or structural weaknesses that could force a business to stop operating. Additionally, coded welding ensures that the pipework is constructed to a high standard and can be used continuously. By investing in coded pipe welding, industries can reduce downtime, extend the lifespan of their pipework, and optimise their efficiency in the long run.
Compliance with Industry Standards
Coded pipe welding ensures that industrial pipework meets strict industry regulations, such as BS EN ISO. These standards define the procedures, materials, and testing requirements needed to produce strong, defect-free welds that are capable of withstanding high pressures and extreme operating conditions.
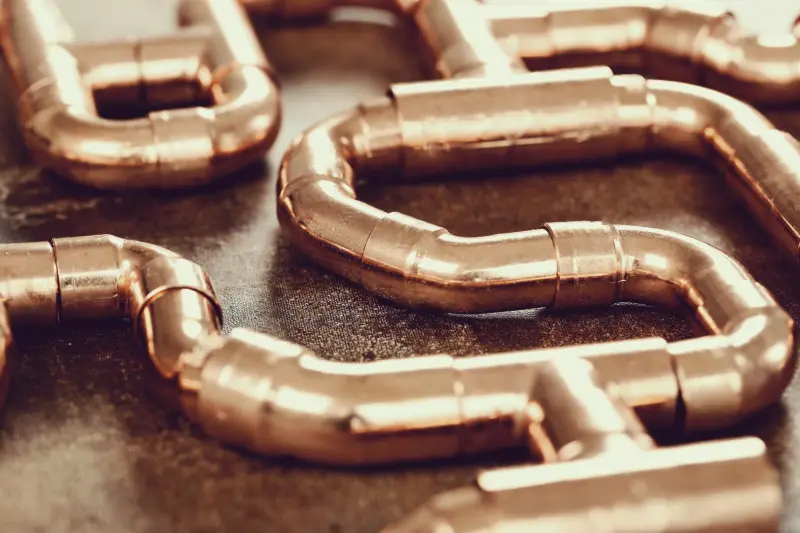
In the UK, industrial pipework must comply with strict regulations in order to minimise the risk of structural weaknesses in the pipework, leaks and even explosions. Coded welders follow industry-approved techniques to produce high-quality, defect-free joints that meet safety standards.
By following these processes, industries reduce risks, extend the lifespan of their pipework, and maintain compliance with UK safety laws. Authorities and regulatory bodies often require proof of compliance through certified welding procedures and documented inspections.
Coded welding processes include non-destructive testing methods, such as radiographic and ultrasonic testing, to verify the integrity of each weld. These testing methods ensure the pipework complies with safety laws and operates efficiently under demanding conditions.
Anderson Engineering And Welding Services provides high-quality welding services for high-pressure and industrial pipelines. We use certified techniques to provide strong, durable welds that meet industry standards.